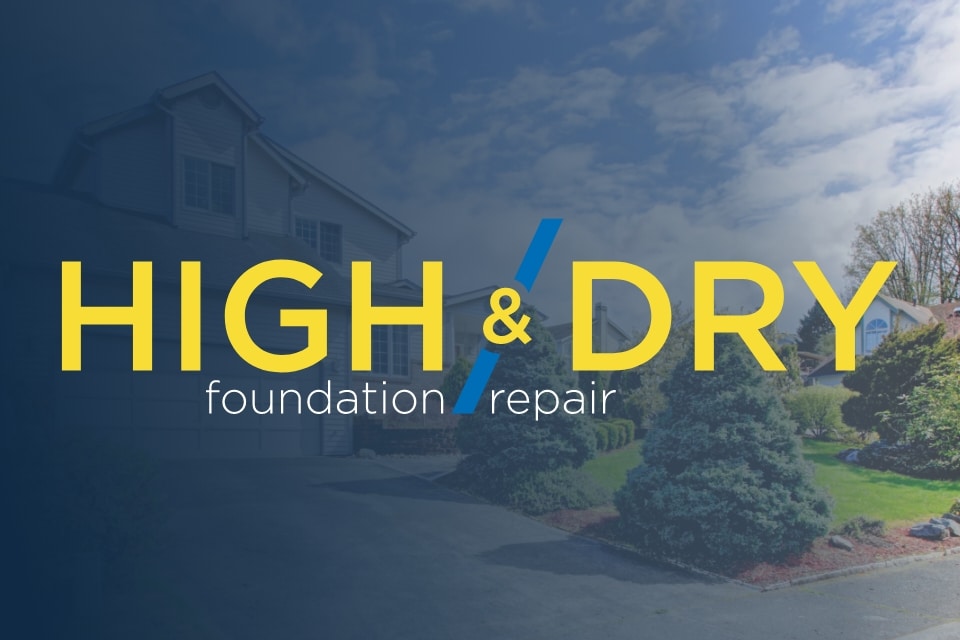
Structural stability is an ever-present battle for homes in and around St. Louis. The combination of expansive soil and extreme seasonal weather changes cause many homes to shift. One common structural concern found in St. Louis basements is lateral wall movement.
When a wall moves laterally, the weight outside of the home becomes greater than the strength of the structure to remain stable. When a wall undergoes this type of pressure it pushes into the basement, creating a visual lean or bow in the wall. Once a wall has started moving laterally into the basement, its strength is compromised and it becomes more susceptible to continued movement. Left alone, walls can lean up to 3” and beyond. Most structural engineers recommend a wall with over 3” of lean be fully excavated outside and pushed back. This process can cost tens of thousands of dollars and take multiple weeks to complete. Therefore, it is important to address the lean as soon as possible.
There are three main repairs used in bracing a wall with a lean or bow: (A) Anchors, (B) Beams, (C) Carbon. Like everything, there are pros and cons to each. Below, each method will be described followed by some recommendations.
Anchors are commonly referred to as plate anchors or tie-backs. There is often a large steel plate inside the basement with a hole in the middle of the plate. A steel rod is placed through that hole and through a drilled-out hole in the foundation wall. This rod continues through the yard about 12’ away from the house where it is attached to a steel bracket encased in concrete. There are different variations of anchors but they share the same basic philosophy; tie the wall to something that is less likely to move underground, outside of the wall.
Here in St. Louis, we at High & Dry only install anchors as a last resort. Sometimes there is no good way to secure the top or bottom of the wall (more about that later) and the only leverage that can be created is to tie the wall to something outside of the home. However, this is the least preferred option given every hole drilled for the anchors is a potential source of leaking. Also, because this process requires excavation outside, there will be a need for landscaping to restore the yard.
Beams are commonly referred to as solider beams or power braces. This process places a large I-beam in front of the leaning wall. The beam is seated in concrete below the floor and steel angle iron hangs off of the floor joists to hold the top of the beam. Not every company secures the bottom and top of the beams the same way but the same philosophy exists: the steel beam is strong enough to not bend when the wall is pushed. This process uses the weight of the house to keep the beams from leaning at the top.
While beams are not as intrusive as anchors, for a prospective buyer, they are visually the most unsettling. Of the three wall bracing systems, beams take up the most floorspace. Given these issues, beams are only recommended when carbon is not an option.
Carbon Fiber is a great alternative to the steel products for many reasons. Carbon fiber is stronger than steel and non-corrosive. It is the least intrusive process of the three describe here and can often be installed in a day and a half. The basic concept is carbon does not stretch, so, when the carbon is chemically bonded to the wall with a high-grade epoxy, the wall will not be able to force the carbon to move. Much like beams, carbon fiber will utilize the weight provided by the floor joist to keep the top of the wall from leaning. (Learn more at fortressstabilization.com)
This system does have its limits but if installed correctly the risk of failure is statistically non-existent. Since the straps are epoxy-glued directly to the wall, it is important to measure the lean/bow of the wall so the carbon is not installed with an aggressive bend. Straps lose strength when significantly curved or bent. When a wall is caught before the lean is beyond the manufacturer’s recommendations, carbon fiber straps are the favorite option at High & Dry Foundation Repair. Here in St. Louis, we use straps from Fortress Stabilization Systems and a lifetime of the structure is often provided by us and the manufacturer.